Materials, suppliers and rebates
Construction supply chain: Everything to know in 2024
By Debbie Trecek •
Published Jun 1, 2023,
updated Feb 16, 2024

In the fast-paced construction industry, effective supply chain management is crucial for optimizing timelines, controlling costs and ensuring project success. By leveraging key strategies and advanced technologies, construction businesses can streamline their supply chains and enhance visibility, coordination and profitability.
To accomplish this, it’s important to explore the components of a construction supply chain, look at emerging trends and highlight best practices. Using this information, builders can improve supply chain management under any market condition.
- What is supply chain management in construction?
- What are the key components of a construction supply chain?
- Construction supply chain trends in 2024
- Best practices for construction supply chain management
- Overcoming construction supply chain challenges in 2024
- How Buildertrend helps with construction supply chain management
- Construction supply chain FAQs
What is supply chain management in construction?
Supply chain management (SCM) in construction refers to the planning, coordination and optimization of the flow of materials, information and finances across the construction project lifecycle. It involves managing the sourcing, procurement processes, logistics and delivery of construction materials and services required for projects.
By effectively managing the supply chain, construction business owners can experience improved timelines and cost savings, while increasing productivity and construction quality.
What are the key components of a construction supply chain?
Building a strong supply chain in construction involves optimizing people-related components alongside activity-related components.
Key people-related components of supply chain management
- Manufacturers: They’re responsible for transforming raw materials into finished goods – such as steel beams or HVAC systems – needed for construction. The availability of these materials can affect supply chain timelines as well as construction quality.
- Suppliers: These are individuals or businesses that provide raw materials and equipment for construction projects. Selecting reliable suppliers ensures your ability to procure quality materials when you need them – and within budget.
- Purchasing programs: These help construction companies improve purchasing power so materials and supplies can be procured at better prices and terms.
- Contractors: They’re responsible for managing the construction process, including overseeing subcontractors and identifying resource needs for successful project execution.
- Subcontractors: They’re responsible for performing specific tasks within a construction project, such as electrical work or carpentry. It’s important to coordinate with subcontractors about their supply chain needs to ensure the overall budget stays on track.
- Logistics providers: These individuals handle the transportation, storage and distribution of materials and equipment. They play a critical role in ensuring items are delivered to a construction site – and in good quality – while minimizing routing costs or transportation delays.
- Project managers: They’re responsible for defining project requirements, objectives and timelines. This includes ensuring building materials, equipment and resources are available when needed by coordinating with the other parties in this list.
Key activity-related components of supply chain management
- Inventory management: Proper inventory management involves tracking and controlling the quantities of materials and equipment on hand. This can help reduce the risk of shortages or wasted materials.
- Demand forecasting: This involves estimating future material and equipment requirements based on project schedules, construction supply management data and market trends.
- Quality control: This ensures materials, equipment and labor are meeting project standards. In supply chain management, quality control is an important step in reducing reordering of materials or rework at a job site.
- Sustainability efforts: Many construction companies are working to reduce waste and source materials in environmentally friendly ways. Sustainable construction jobs may affect procurement activities, including supplier selection and logistical delivery.
Construction supply chain trends in 2024
Buildertrend’s recent construction outlook report describes several key construction trends for 2023, especially in relation to construction supply chain issues.
1. Increasing labor availability
It’s predicted the availability of construction workers will gradually improve in 2023. Even with these improvements, costs may not be significantly lowered. This suggests the labor shortage will remain a challenge but may be less severe than the past few years.
This is an important consideration for supply chain management, as a shortage of labor can affect pace of work and reduce overall efficiency and productivity of the supply chain.
2. Reliance on subcontractors
To address the labor shortage, construction businesses are increasingly depending on subcontractors to handle work they don’t have the capacity to complete in-house.
This suggests it will be critical to strengthen subcontractor relationships to ensure project success. Effective supply chain management will involve coordinating with multiple subcontractors to ensure smooth communication, timely delivery of materials and trust in quality control throughout the construction process.
3. Material delays and rising costs
Building material delays and rising costs have been disruptive factors for construction projects in recent years. While some larger builders have mitigated this challenge by entering into long-term contracts to secure supply, this has led to even more delays for smaller builders. It’s expected that some delays will continue in 2023.
4. Proactive procurement planning
Due to the challenges listed above, there is a growing trend of builders developing proactive plans for procuring materials. This includes evaluating current vendors, considering new options and joining purchasing programs to help increase purchasing power.
Current housing market trends show that construction supply chains, especially building material supply chains, will likely continue to become more complex. This is because of ever-changing shortages and market demands, including things as seemingly simple as home builder design trends.
Increased adoption of technology can streamline supply chain management, enabling better coordination, transparency and efficiency in material procurement and delivery.
Best practices for construction supply chain management
Effective supply chain management is a crucial part of meeting project timelines, controlling costs and meeting client expectations. To accomplish this, here are seven tips to help you navigate the construction supply chain with greater efficiency and success.
1. Enhance communication and coordination
Establishing clear communication channels among all parties is essential for ensuring visibility and coordination within the construction supply chain. This promotes effective collaboration and minimizes delays or miscommunications that can impact the flow of materials and information.
2. Select reliable suppliers and subcontractors
Be diligent when selecting suppliers and subcontractors. Evaluating their capabilities, reliability and financial stability helps ensure that they can meet the project’s requirements and contribute to smooth operations. Supplier relationship management is crucial for maintaining a reliable and resilient construction supply chain.
3. Optimize inventory management
Implementing strong inventory management practices allows builders to optimize procurement, transportation and storage of materials and equipment. This involves efficiently tracking inventory levels, anticipating demand and coordinating deliveries to minimize delays and excess inventory.
4. Leverage technology solutions
Investing in technology solutions – such as construction software – helps improve visibility, traceability and efficiency in managing the construction supply chain. These tools provide real-time data, streamline processes and facilitate better decision-making.
5. Ensure quality control
Implementing strict quality control processes – including regular inspections, testing and documentation – is vital for maintaining high standards of materials and workmanship. This helps prevent costly rework, delays and potential issues that could arise from using subpar materials.
6. Develop contingency plans
By planning ahead for disasters, disruptions or changes in project scope, builders can proactively devise alternative strategies and minimize the impact on the overall supply chain.
7. Foster collaboration and trust
Coordinating closely with all parties involved in a project – home builders, suppliers, subcontractors and project team members – fosters a culture of collaboration and mutual trust. Open and transparent communication helps you identify supply chain needs before they can become a disruptor to your timeline.
Overcoming construction supply chain challenges in 2024
Overcoming construction supply chain challenges isn’t easy. Technology can help streamline several processes and problems that you might experience along the way, such as:
Fragmented supply chain
Digital communication tools help support better communication between different stakeholders in the supply chain. This can allow for real-time information sharing, which will streamline processes, reduce errors and improve coordination between suppliers, subcontractors and builders.
Material availability and lead times
Technology can provide builders with insights into material inventory levels, shipments and supply chain disruptions, such as delays on delivery. It enables proactive procurement planning and sourcing, helping builders mitigate risks associated with material shortages and long lead times.
Seasonal demand and weather conditions
Scheduling software enables builders to efficiently adjust task schedules when weather conditions change. This way, builders can easily reschedule tasks, even factoring for how those adjustments might affect dependent tasks. This maximizes your timeline, ensuring work is being done – rain or shine.
Cost management
Financial tools within construction management software can track costs so builders can monitor project expenses, track budgets and identify opportunities to save. Automated tools streamline financial processes, reduce manual errors and help deliver projects within budget.
Quality control
Construction technology helps improve task management, allowing project managers to create and assign tasks to team members. This means that if something is caught on an inspection, your team has time to adjust before closeout. Additionally, construction software enables real-time collaboration and communication among team members, ensuring everyone is on the same page and can address quality issues promptly.
Risk mitigation
Construction software helps builders reduce risk by providing features such as document management. This ensures all project-related documents – contracts, permits, change orders – are easily organized, accessible and securely stored. This helps prevent errors and disputes during a project.
Technology-driven project tracking is another method of reducing builder risk. This feature helps lower the chances of project delays and overruns by identifying potential bottlenecks and resolving them quickly.
Training and development of technology adoption
Training and support programs can assist builders in adopting and effectively utilizing technology solutions. Training sessions – including Onsite Consulting – combined with user-friendly interfaces make it easier for construction professionals to incorporate technology into their workflows. This makes it easier for them to spot and resolve potential supply chain challenges.
Sustainability and resilience
By prioritizing sustainability in the sourcing of supplies and materials, construction companies can contribute to reducing waste and minimizing their long-term supply chain needs. This can be achieved by seeking out eco-friendly and recycled materials, implementing waste reduction strategies and partnering with suppliers with sustainability goals. Incorporating sustainable practices helps environmental conservation and the overall efficiency and resilience of the supply chain.
How Buildertrend helps with construction supply chain management
Buildertrend can help construction businesses manage their supply chains through our comprehensive construction company software. Specifically, this includes features like:
- Buildertrend Takeoff, which ensures accurate material estimation to help optimize inventory levels and reduce waste.
- Scheduling software, which provides comprehensive oversight of project timelines, enabling builders to plan and coordinate with suppliers efficiently.
- Construction finance software, which offers real-time visibility into estimates, project costs and cash flow, helping builders maintain profitability and adapt to volatile supply costs.
- Integrated purchasing programs, which help builders secure premium supplies at lower rates, manage vendors and track orders with ease.
By harnessing Buildertrend’s expert technology, you can streamline procurement, improve collaboration with suppliers and maximize your operations – even when supply chain trends are challenging
Construction supply chain FAQs
Check out these answers to common questions about construction supply chain management.
Sustainability can be integrated into the construction supply chain by sourcing sustainable supplies and materials, implementing green building practices and promoting recycling and waste reduction throughout the construction process.
Read more about how Buildertrend specifically supports sustainable construction companies in this case study.
Risk management can be integrated into construction supply chains by developing contingency plans, conducting thorough due diligence when selecting suppliers, implementing quality control processes and leveraging technology solutions to enhance visibility and accountability.
There are several benefits of supply chain management in the construction sector:
- Cost reduction: Efficient management of the supply chain reduces costs associated with delays, excess inventory or wastage.
- Project timelines: Supply chain integration ensures timely delivery of materials, preventing project delays.
- Quality control: Successful supply chain management helps in ensuring the quality and reliability of material management and services.
- Risk management: It minimizes risks related to disruptions in the supply chain.
Earn rebates, build supplier relationships
Buildertrend: The one platform where you can manage both projects and purchases.
Want to stay updated?
Subscribe to our newsletter
About The Author
Debbie Trecek Debbie Trecek is a freelance copywriter for Buildertrend.
Construction material management guide
Effective construction material management helps ensure that supplies are available, reducing delays and keeping your projects on schedule. Learn more here.
Construction procurement guide
Construction procurement is the process of acquiring goods and services for construction projects. Learn more about the steps involved here.
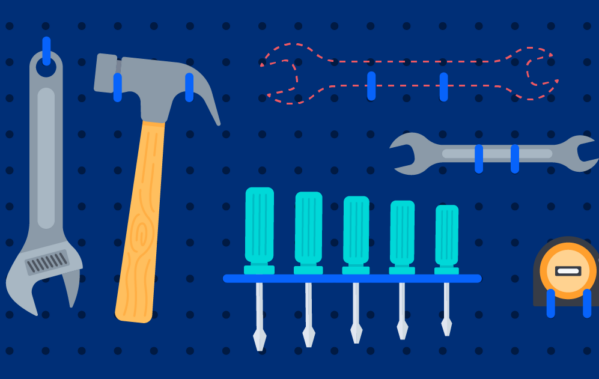
How to track construction equipment easier
Home builders and remodelers need to be able to track construction equipment. Here’s how to make it easy with Buildertrend.
Want to contribute to our blog?
We believe in building a community for construction – sharing is a big part of that. If you have industry expertise or a story to tell, your voice can reach thousands here.