Materials, suppliers and rebates
Construction materials management: Definition, best practices & more
By Madyson Alger •
Published Sep 6, 2023,
updated Feb 29, 2024

Let’s dive into the best and newest practices for material management in 2023. We’ll discuss familiar supply chain challenges and propose possible solutions. When it comes to managing materials, there’s always room for improvement.
- What is construction material management?
- What is construction material management software?
- Why is construction material management important?
- 6 construction material management strategies
- 3 challenges to overcome in construction materials management
- 4 best practices for construction materials management
- How Buildertrend helps manage construction materials
- How do rebates work within Buildertrend’s construction material management software?
- Construction material management FAQs
What is construction material management?
Construction material management is the systematic planning, procurement, storage and control of materials during a construction project. It involves tasks such as identifying material requirements, sourcing suppliers, managing inventory and handling transportation.
What is construction material management software?
Construction material management software is a digital tool that helps business owners and project managers streamline their material management process for construction projects. A successful construction manager can implement a software to help reduce material costs through rebates, organize inventory, track orders and schedule deliveries.
Why is construction material management important?
Effective construction material management is important for maximizing productivity, increasing accuracy, improving communication and combating inflation.
As a home builder, chances are you’ve been affected by supply chain disruptions and escalated material costs. Planning ahead reduces these risks – plus it cuts down wait time and helps manage inventory.
Maximizing productivity
Construction material management software is a great tool for maximizing productivity. It helps contractors like you track and manage the materials needed for projects. This software can also create detailed reports – ensuring no materials are wasted – and keep track of inventory levels, so new materials can be ordered in time for upcoming projects. You can quickly and accurately estimate material costs and ensure you have enough of what you need when you need it.
Increasing accuracy
With construction software, you’re not only able to improve efficiency, but you can also increase accuracy. You can manage materials for each project – from initial order to delivery. This software also helps track materials being used, ensuring all materials are accounted for and that you’re less likely to over or underbuy. You can better manage your inventory and know you always have the right number of materials on hand when needed.
Improving communication
This type of software can also help you improve communication between stakeholders and your team by providing real-time updates. It makes it easier to provide the status of materials, measurements for projects and updates on inventory. Construction companies can also save time and improve communication by streamlining processes and reducing manual errors in the data entry process.
Combating inflation
Material management is also essential for combating inflation by providing accurate and timely data on material costs. This allows businesses to make informed decisions about their purchases and ensure they’re not overspending. Additionally, material management can provide insight into potential savings opportunities through group purchasing. This information can then be used to make adjustments to the budget, which will help control the pressure of inflation.
6 construction material management strategies
Implementing the right strategies for construction material management can help your business with timely project completion and cost-effectiveness. Here are six strategies you can use to manage materials.
1. Accurate project planning
Thoroughly planning a project to determine the exact quantity and types of materials will help to avoid over or underordering. This also reduces waste and minimizes costs.
2. Centralized procurement
Centralizing the procurement process will streamline material sourcing. With this strategy, you can maintain a list of approved suppliers and negotiate long-term contracts to ensure a steady supply of materials at competitive prices.
3. Inventory management
Implementing an inventory management system to track and monitor material stock can be a helpful strategy to prevent excess or low inventory. In this process you’ll update the inventory, conduct stock audits and establish reorder points.
4. Efficient material storage
Optimizing storage can be helpful for keeping up with material inventory. With this strategy, you’ll categorize and label materials for easy identification and ensure proper handling techniques to prevent damage or deterioration.
5. Supplier relationships
Developing strong relationships with suppliers will create trust and reliability. You can regularly communicate project requirements, timelines and quality expectations to keep a smooth material management process.
6. Technology and automation
Implementing construction management software to streamline material management processes is crucial. Software will help you with inventory tracking, procurement and project planning – digitally. This enhances accuracy and efficiency for your business.
3 challenges to overcome in construction materials management
The top material management challenges facing construction companies are:
1. Inaccurate material forecasting
Exact, or as close as possible, construction forecasting benefits your financials. An inaccurate material forecast results in an over or undersupply of materials.
If accuracy is the goal, skip the pen and paper – a good construction takeoff software will cover you on all the nitty-gritty details. Plus, your material amounts and costs will be available to reference on future orders.
2. Improper storage
When materials arrive too early … they sit. And when left exposed to the elements, there’s a chance of weather damage or theft. Depending on the size of the job and of your business, you may not have a secure, covered storage option.
3. Coordinating material deliveries with construction schedules
Planning leads to productivity. Without strict attention to schedules, your team is left moving materials from point A to point B when they should be making headway on the job.
Material deliveries need to happen when your project manager is there to inspect everything and make the call on the closest storage option. Relocating materials wastes labor time and can also lead to wear and tear.
4 best practices for construction materials management
Follow these guidelines to save time and money and to responsibly dispose of material waste:
1. Develop accurate material forecasts
When forecasting, first know your inventory. Conduct regular checks and promptly use leftover materials.
Research the market to know which materials are causing delays, plus follow industry trends and buy when prices on certain materials are low. Choose materials that are in stock and shipped to your job site as soon as possible. Estimating in construction isn’t easy, but it protects your job profits. Accurate counts on material costs and volume save you time, money and extra labor.
2. Implement proper storage and handling procedures
Even if you meticulously plan ahead with an organized delivery schedule, chances are you’ll still need a safe storage option at some point. If the job site is secure from theft and damage, your first option is to store everything there. High-value raw materials such as copper wiring should never be left unattended.
If you need a short-term warehouse, consider renting near the field. When storing your supplies, document every detail. This includes how much you have, where it’s stored, the job site it’s for and who handled it.
3. Coordinate material deliveries with construction schedules
Accurate scheduling reduces the time your materials will be sitting unused. The quicker the materials are used, the lower the chance of something happening.
Also, a healthy supplier relationship can help keep you on schedule. Learn more here.
4. Ensure proper disposal of construction waste
Consider donating unused materials. Many local companies accept building material and appliance drop-offs. If you have leftover or gently used lumber or kitchen cabinets, donating is the best option.
Items like paints and electronics are considered hazardous materials, and the EPA has directions on how to properly dispose of these. If your supplies don’t fit in the above categories, then recycle or bring them to a landfill as it’s appropriate.
How Buildertrend helps manage construction materials
Buildertrend is No. 1 when it comes to construction material management software. Use these project management tools to keep tabs on materials:
- Daily Logs show a detailed recording of exactly where you are in a project and an idea of its pacing for the most accurate material delivery timeline.
- Change Orders are necessary for saving electronic signatures if you end up facing a construction claim. These signatures are your backup if delayed materials (due to a change order) are holding up your project.
- Schedules help in planning projects, keeping jobs moving and showing updates. Sync material delivery with your project schedule.
- Purchasing eases the process of managing rebates and getting returns on products.
How do rebates work within Buildertrend’s construction material management software?
Buildertrend Purchasing can help you manage rebates to save money, keep a competitive advantage in your market and increase purchasing power. You can follow these three steps when signing up for rebate programs through Buildertrend.
- Enroll in supplier rebate programs: After finding programs you’d like to enroll in, you’ll view items eligible for rebates, read their terms and then sign up.
- Upload your receipts: Add your receipts for purchases made through suppliers, and we’ll make it easy by automatically scanning product SKUs for eligible rebates. You’ll then review each rebate and submit.
- Set up Buildertrend Wallet: Buildertrend Wallet is our newest financial tool that will allow you to collect your rebates. You’ll receive funds quickly within your Buildertrend account and spend them however you’d like.
Get started with Buildertrend by scheduling a demo today.
Construction material management FAQs
Get answers to the most common construction material management questions.
Improve your construction material management by conducting a forecast, ordering accurate amounts and scheduling products to arrive exactly when you need them. Avoid storing or wasting materials whenever possible.
Minimize the waste of construction materials with a detailed forecast of the exact count of supplies needed for each job. Planning costs and materials on an accurate estimate is the best way to reduce waste.
Construction material management directly impacts a project’s budget because the less material used on a project the less it costs you. Overspending happens when the product gets delayed or you have a material surplus. Double and triple check that you’re ordering the correct product – making mistakes also impacts the budget. Â
Sustainability plays a significant role in construction material management. If you order too much, the wrong product gets delivered or it gets damaged in handling – everything gets tossed into the landfill. Avoid this with forecasting, knowing your inventory and aligning the delivery and project schedules.
The best way to track materials on a construction site is to use a material tracking software or app that allows you to input data such as material type, quantity, location and usage. It’s important to have a system in place to ensure that materials are being used efficiently and effectively.
Want to stay updated?
Subscribe to our newsletter
About The Author
Madyson Alger
Construction supply chain: Everything to know in 2023
Managing a construction supply chain can be complex. Find out everything you need to know to manage supply chains and overcome challenges.
Construction procurement guide
Construction procurement is the process of acquiring goods and services for construction projects. Learn more about the steps involved here.
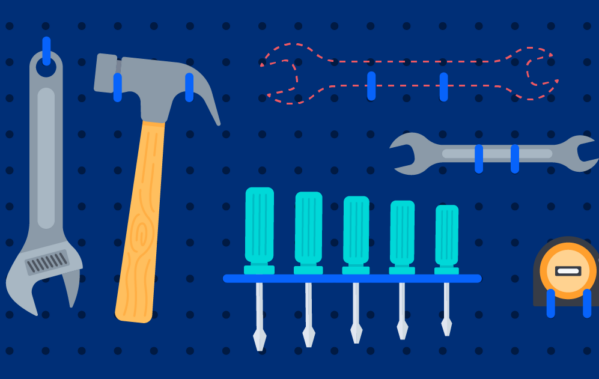
How to track construction equipment easier
Home builders and remodelers need to be able to track construction equipment. Here’s how to make it easy with Buildertrend.
Want to contribute to our blog?
We believe in building a community for construction – sharing is a big part of that. If you have industry expertise or a story to tell, your voice can reach thousands here.